In the middle of the Artificial Intelligence (AI) hype, our February 28th webinar, “Leveraging AI to Improve Quality in Manufacturing,” sought to demystify AI and Computer Vision (CV) for the manufacturing sector. The session was not merely about celebrating these technologies but offering a pragmatic lens through which we examined their application in enhancing manufacturing quality management.
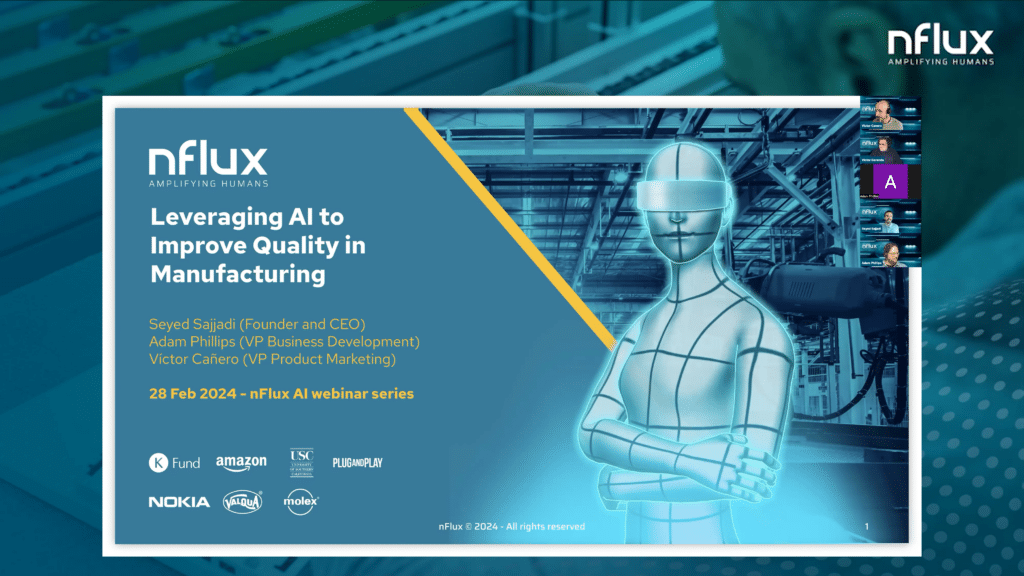
This post recaps the core themes discussed during the webinar, aiming to shed light on how AI and CV can tangibly benefit the manufacturing process. From exploring the basics of AI in CV to examining its applications and understanding the Cost of Quality (CoQ), we delve into how these innovations are reshaping the industry.
The Role of AI in Computer Vision
We initiated our discussion by explaining the critical role of Artificial Intelligence (AI) and Machine Learning (ML) in enabling machines to interpret and analyze visual data. While computers excel at executing repetitive tasks quickly and accurately through algorithms (commonly referred to as computer programs), interpreting digital images or video feeds in real time is complex. Recent advancements have leveraged neural networks and other cutting-edge techniques, combined with ML, to enable computers to autonomously generate algorithms capable of extracting meaningful information from visual data. This advancement marks a cornerstone in the Machine Learning domain.
The computer vision journey begins with “training,” where a computer learns to recognize various objects from a vast collection of images and videos, known as the “Training Dataset.” This process culminates in the creation of an AI model, which down below is just a sophisticated automatically generated algorithm, which enables to computationally identify patterns and features within these datasets. These datasets, comprising labeled or annotated images or video frames, are meticulously prepared to ensure accurate learning.
Key Tasks in Computer Vision: Segmentation, Object Detection, and Classification
We then provided a brief description of the different tasks that AI models within Computer Vision are trained to execute, each with its unique purpose:
- Segmentation: This process divides an image into segments for easier analysis. In manufacturing, segmentation can distinguish different components on a conveyor belt, enabling individual analysis.
- Object Detection: Beyond segmentation, this task identifies and locates objects within the segments. Its importance is paramount in applications like defect detection on production lines, where pinpointing flaws is crucial.
- Classification: This involves categorizing objects within an image into predefined classes, determining whether an item meets specific criteria, such as quality checks.
Training an AI model is an intricate process. For engineers and technical professionals in manufacturing, grasping the foundational concepts behind Computer Vision training is essential for effectively leveraging AI and Computer Vision. While manufacturers venturing into Computer Vision need not become data scientists or CV experts, understanding the technical and operational facets of CV training is vital. This knowledge directly influences the precision of AI models, thereby affecting the efficacy of the solutions utilizing these models.
Computer Vision Training is a compelling topic, where we, at nFlux, possess extensive expertise. The development and application of AI and Computer Vision in manufacturing strike a balance between technological sophistication and practical utility. Although the underlying algorithms and models are complex, their ultimate goal is straightforward: to boost manufacturing efficiency, safety, and quality. We’re considering exploring Computer Vision Training in more depth in future webinars or blog posts or webinars. Let us know in the comments if this is something you’d like us to delve into further.
Key applications of Computer Vision in Manufacturing
Our deep dive into CV applications continued to reveal its transformative impact across multiple aspects of manufacturing:
- Worker Safety and Ergonomics: One promising application of Computer Vision is in enhancing worker safety and ergonomics. Through real-time and ex-post analysis of worker posture during heavy-lifting and assembly processes, Computer Vision systems can identify potential safety risks and ergonomic issues. By alerting supervisors and workers to dangerous postures and suggesting corrective actions, these systems help reduce the risk of injuries and improve overall workplace safety.
- Worker Training: The acceleration of training time and the potential reduction in worker attrition are significant benefits of applying Computer Vision in worker training. State-of-the art developments are closer to the entertainment industry (aka video games) than to manufacturing industry, with too much effort being made on building costly virtual scenarios, AR/VR and haptic interfaces, but little attention to the inherent variability of procedure executions by different workers and the need to generate training scenarios very fast, and at a reasonable cost. In this regard, it is worth mentioning nFlux’s successful approach to worker training using a more simplistic approach with Worker Guidance. If you are interested in learning more download the Whitepaper on how Nokia is using artificial intelligence to train workers on the shop floor.
- Cycle Time Measurement and Process Optimization: Accurate measurement of task times and production output in real-time is another critical application. Computer Vision technologies integrate with Manufacturing Execution Systems (MES) and Enterprise Resource Planning (ERP) systems, elevating them to new levels of performance. By providing detailed insights into the production process, these systems enable manufacturers to identify bottlenecks, streamline operations, and optimize cycle times, thereby enhancing productivity and reducing costs.
- Defect Detection and Advanced Optical Inspection: High-precision defect detection is crucial in maintaining quality, especially in continuous mass production industries. Computer Vision facilitates advanced optical inspection through specialized hardware, allowing for the detection of minute defects that might be missed by human inspectors. This capability ensures that products meet quality standards, reducing waste and rework, and ultimately, protecting the brand’s reputation.
- Worker Guidance: Providing real-time guidance and on-the-spot error correction for workers in discrete manufacturing environments is the latest trend in the application of CV to manufacturing. This system offers immediate feedback to workers, helping them correct errors as they occur and preventing defects before they happen. By moving Quality Inspection upstream, to the very place where defects are generated, not only improves product quality but also enhances learning and efficiency on the production floor.
During the webinar we made a live demo of nFlux Guide™, our innovative solution for worker guidance, from our Lab in Salt Lake City, UT. Unfortunately, due to time constraints we couldn’t go deeper into the benefits of moving from discrete instant inspection to continuous worker guidance, but we are going to host a webinar specifically for this: If you are interested you can sign up to the webinar “Boost Yield and Quality by Upstreaming Inspection with AI” to be held on March 13th. It is also worth mentioning the insightful Whitepaper that we published with Nokia on how they used AI to optimize Quality in their shopfloor.
We invite our readers to share their thoughts and interests on these topics. Your feedback could shape our future deep dives, helping us focus on the areas of greatest interest and potential impact.
Decoding Cost of Quality
The last topic we devoted quality time to was decoding the intricate landscape of the Cost of Quality (CoQ), which unveils a significant financial consideration for manufacturers, often accounting for 20-30% of revenues (according to nFlux customers). This multifaceted metric includes both tangible and intangible elements that, in many companies, is accounted for across different departments and sections, making it challenging to gain a comprehensive understanding of the total CoQ. This fragmentation often obscures the full impact of quality-related expenses, complicating efforts to optimize operations and improve product quality and prevent impact to the bottom line.
These are the key components of CoQ:
- Prevention Costs: This category, making up 15-30% of the total CoQ, is invested in avoiding defects before they occur. It includes quality planning, standards training, process control and improvement, and supplier quality management. Investments in prevention are foundational to maintaining high-quality standards and reducing the likelihood of defects.
- Appraisal Costs: Accounting for 25-40% of CoQ, appraisal costs are incurred to assess and ensure products meet quality standards. This includes inspection and testing, quality audits, and any activities designed to catch defects before products reach the customer. Excessive appraisal costs suggest a reliance on catching problems rather than preventing them.
- Internal Failure Costs: These costs, representing 15-25% of CoQ, arise from defects found before a product reaches the customer. It includes scrap, rework, and process failure reduction strategies, indicating areas where improvements in prevention could reduce waste.
- External Failure Costs: At 20-30% of CoQ, external failure costs occur when defects are discovered after the product has reached the customer. This category includes warranties, returns, complaint handling, and product liabilities, affecting both financials and brand reputation.
Understanding these costs is pivotal for manufacturers aiming to streamline operations and enhance product quality. AI and Computer Vision technologies offer an opportunity to significantly reduce CoQ by automating prevention and appraisal activities, improving detection of internal failures before products leave the factory, and minimizing external failures through enhanced quality control measures. Investing in AI-driven improvements can shift the CoQ balance towards prevention, reducing the total CoQ and driving efficiencies and savings that directly impact the bottom line.
If you really want to optimize your cost of quality, you need to start measuring it … after several conversations with customers and prospects, we learnt that cost of quality is scattered throughout different departments of the same organization, and that’s why a significant amount of manufacturers do not realize that cost of quality could be up to 30% of their revenues!
Víctor Cañero – VP Product Marketing at nFlux
This deeper dive into the components of CoQ not only highlights the areas where AI can make a substantial difference but also underscores the importance of strategic investments in technology to improve manufacturing outcomes. Let us know if this breakdown clarifies the potential impact of CoQ on your operations and how we might explore solutions to optimize these costs further.
Conclusion and Forward Look
Reflecting on the webinar, it’s evident that AI and CV are not just futuristic concepts but present-day tools driving significant improvements in manufacturing. By understanding and applying these technologies, manufacturers can enhance efficiency, safety, and quality across their operations. As we continue to explore these advancements, we invite the community to engage with us, sharing their insights and interests to shape future discussions.
As the industry evolves, so too will the application of AI and CV in manufacturing. Staying informed and open to innovation will be key to leveraging these technologies to their fullest potential. Join us in our journey of discovery and application, as we unlock new levels of operational excellence together.
One Response